De-icing Methods and Working Principles: Innovations by a Leading Block Ice Machine Maker
March 25, 2025
In industrial ice production, efficient de-icing is critical to maintaining productivity, minimizing downtime, and ensuring consistent block ice quality. As a trusted block ice machine maker, BAOCHARM integrates advanced de-icing technologies tailored for ice production plants, block ice factories, and facilities relying on ice making equipment. This article explores common de-icing methods, their pros and cons, and how BAOCHARM’s proprietary solutions optimize performance in real-world applications.
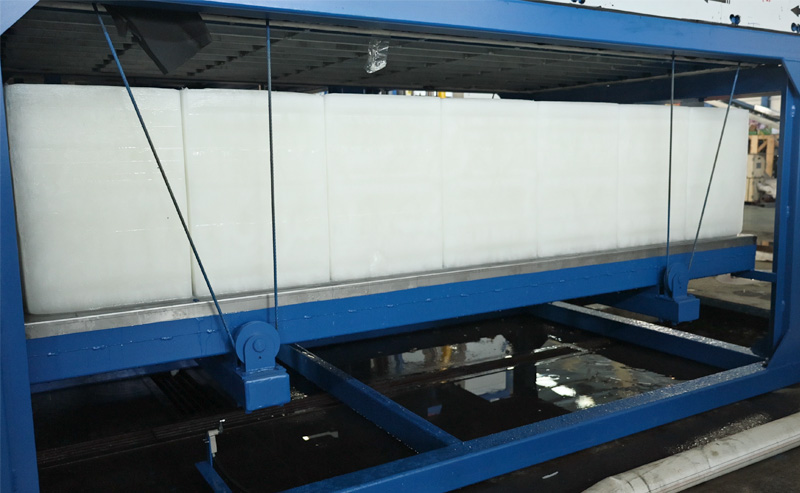
Common De-icing Methods in Industrial Ice Production
Hot Water De-icing
- Process: Warm water circulates around ice molds to melt the outer layer, releasing blocks.
- Advantages: Fast, uniform ice release.
- Drawbacks: High energy consumption; requires precise temperature control.
Mechanical De-icing
- Process: Vibrators or pneumatic tools physically dislodge ice blocks.
- Advantages: Lower energy use; suitable for smaller ice making plants.
- Drawbacks: Risk of ice damage; higher maintenance costs.
Hot Gas De-icing
- Process: Refrigerant gas heats mold surfaces to loosen ice.
- Advantages: Energy-efficient; preserves ice integrity.
- Drawbacks: Requires specialized ice maker making machine designs.
How BAOCHARM’s De-icing Technology Works
BAOCHARM combines hot gas and smart automation to deliver a hybrid solution. Here’s the workflow:
- Pre-cooling Phase: The system stabilizes mold temperatures to ensure uniform ice formation.
- Controlled Heating: Refrigerant gas warms molds just enough to create a micro-layer of water between the ice and mold.
- Automated Ejection: Sensors trigger gentle mechanical ejection, ensuring intact, smooth-surfaced blocks.
This method reduces energy use by 25% compared to traditional hot water systems while minimizing wear on ice making equipment.
BAOCHARM De-icing in Action: Case Studies
Case 1: Large-Scale Ice Production Plant in Southeast Asia
- Challenge: A 20-ton/day block ice factory faced frequent downtime due to slow de-icing.
- Solution: BAOCHARM installed a hot gas de-icing system with IoT-enabled temperature controls.
- Result: De-icing time reduced by 40%, with 15% lower energy costs.
Case 2: Fisheries Cold Chain Facility
- Challenge: Mechanical de-icing damaged 10% of ice blocks during ejection.
- Solution: BAOCHARM’s hybrid system eliminated physical contact during ejection.
- Result: Zero ice breakage and 30% faster production cycles.
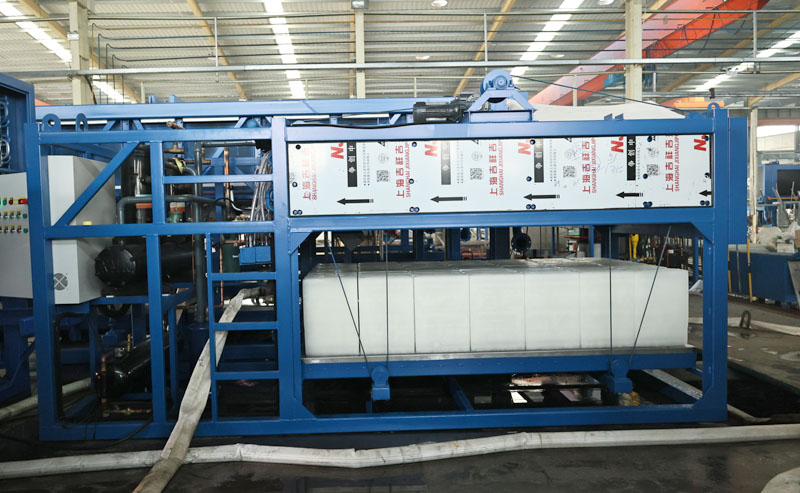
BAOCHARM: The Smart Choice for Industrial-Grade Block Ice Machines
Revised Section Content:
As a pioneer in ice making equipment innovation, BAOCHARM stands out among global block ice machine makers for three key reasons:
- Energy-Saving Precision: Our patented hybrid de-icing systems reduce power consumption by up to 30%, ideal for high-volume ice production plants.
- Long-Term Reliability: Aerospace-grade stainless steel molds resist corrosion, ensuring 10+ years of service in harsh environments like marine fisheries or food processing block ice factories.
- Scalable Solutions: Whether you operate a compact ice making plant or a 50-ton/day facility, we engineer machines to match your output goals and space constraints.
Conclusion
Selecting the right de-icing method directly impacts the efficiency and profitability of your ice production plant. BAOCHARM’s innovative technologies address industry pain points, delivering faster cycles, lower costs, and superior ice quality.
Ready to upgrade your ice making equipment? Contact us today for a free consultation or request a customized quote. Let us help you optimize your ice production process with cutting-edge solutions.