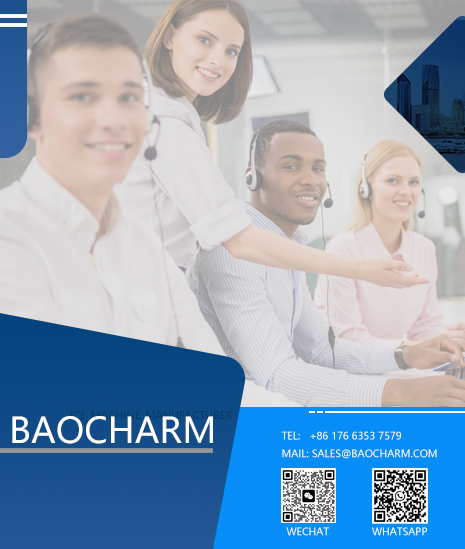
leave a message
If you are interested in our products and want to know more details,please leave a message here,we will reply you as soon as we can.
ice plant refrigeration system
Our Contacts
Email: sales@baocharm.com
WhatsApp: +86 17663537579
Wechat: +86 17663537579
Working Hours: Mon ~ Sat 8:30 AM - 5:30 PM